Metal Stamping Procedures: From Prototyping to Automation
Checking Out the World of Metal Stamping: From Style to Production
Within the world of manufacturing, steel stamping stands apart as a specific and effective technique for forming metal sheets right into numerous types with amazing consistency. From the preliminary design stage where detailed patterns form to the detailed manufacturing procedures, steel stamping is a blend of virtuosity and design. Exploring this globe unveils a complicated interaction of creativity and technological proficiency, supplying a look into a world where advancement satisfies workmanship.
Background of Steel Stamping
Steel marking, a widely utilized manufacturing process today, has an abundant background that dates back to old times (Metal Stamping). The beginnings of metal marking can be mapped to ancient human beings such as the Egyptians, that used stamping techniques to decorate fashion jewelry and ornaments with elaborate styles. Gradually, steel marking evolved, with worlds like the Greeks and Romans using it for creating coins and ornamental products
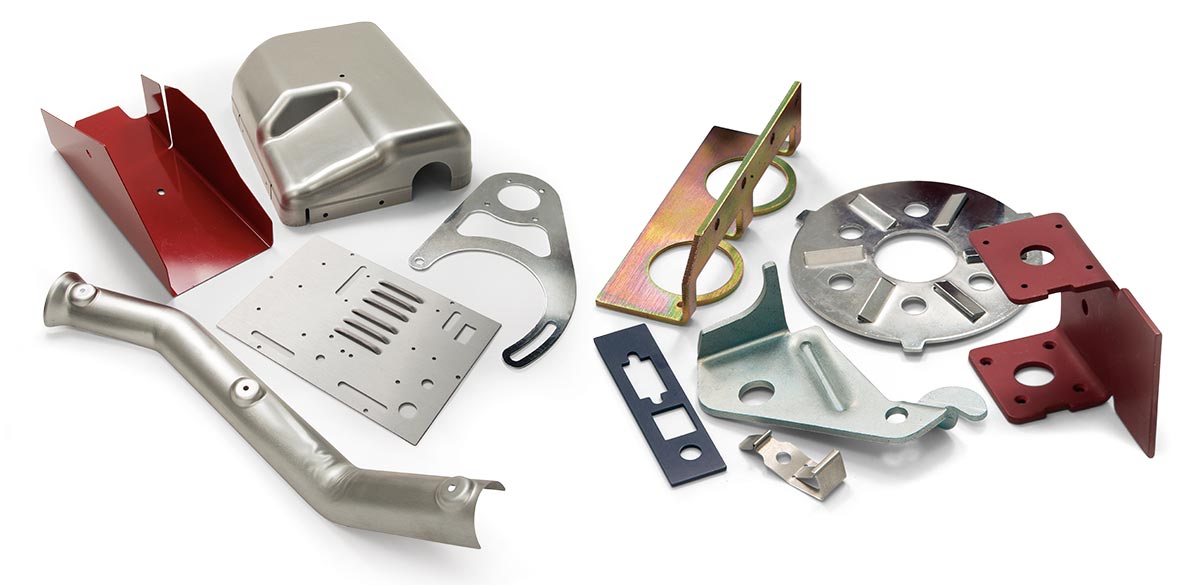
In the 20th century, steel stamping proceeded to progress with the integration of automation and computer numerical control (CNC) technology. These improvements additionally raised the efficiency and precision of steel stamping procedures, making it an essential part of modern manufacturing throughout sectors such as auto, aerospace, and electronic devices. Today, metal stamping continues to be a crucial production procedure, integrating practice with advancement to satisfy the demands of a regularly evolving sector.
Design Factors To Consider and Prototyping
When creating metal marking jobs, meticulous interest to make considerations and prototyping is essential for making certain ideal manufacturing outcomes. Layout considerations in metal stamping include product choice, part geometry, tooling design, and production feasibility. Picking the appropriate material is important as it affects the component's efficiency, price, and manufacturability. Component geometry affects the complexity of the marking process and the functionality of the final product. Tooling layout plays a significant role in the success of metal marking tasks, affecting part accuracy, tool long life, and production efficiency.
Prototyping is a critical stage in the steel marking process that allows engineers to test the layout, confirm manufacturability, and make essential changes before full-scale production. Prototyping aids recognize prospective problems at an early stage, saving time and prices in the lengthy run. It likewise offers an opportunity to optimize the layout for effectiveness and high quality. By thoroughly considering layout elements and utilizing prototyping, manufacturers can simplify the steel stamping procedure and accomplish top quality, cost-effective manufacturing results.
Tooling and Tools Fundamentals
Thinking about the essential duty that tooling layout plays in the success of steel marking jobs, comprehending the vital tools and equipment required is paramount for more tips here attaining reliable manufacturing results. Fixtures hold the metal in area throughout the stamping process, ensuring precision and important source repeatability. Spending in high-grade tooling and devices not only improves manufacturing effectiveness however also leads to greater accuracy, decreased waste, and overall price financial savings in metal stamping procedures.
Production Process and Top Quality Control
Effectively handling the manufacturing procedure and executing robust top quality control procedures are vital for guaranteeing the success of steel marking projects. The manufacturing process in steel marking includes a series of actions that should be carefully collaborated to achieve optimum results. It starts with the preparation of basic materials, complied with by the setup of the marking equipment and tooling. Operators after that feed the materials right into the press, where the marking operation happens. Throughout this process, it is critical to keep track of the assembly line for any type of view publisher site concerns that may influence the high quality of the stamped components.
Quality assurance in steel marking is extremely important to deliver products that meet the required specs. Checking the stamped components at numerous phases of manufacturing assists recognize any kind of issues early on, preventing expensive rework or scrap. Methods such as dimensional assessment, aesthetic assessment, and product screening are generally used to make certain the top quality of the stamped components. By keeping rigorous top quality control criteria, suppliers can promote their online reputation for supplying high-grade steel marked products.
Applications and Sector Insights
In the world of steel stamping, the effective application of manufacturing procedures and top quality control measures directly influences the efficiency and reliability of various industry applications and offers useful understandings into the market's operational dynamics. Furthermore, metal stamping helps with the production of various household appliances, including fridges, cleaning makers, and stoves, by offering affordable services for producing resilient and complex parts. Recognizing the applications and sector understandings of metal stamping is essential for maximizing manufacturing processes and enhancing product top quality throughout different sectors.
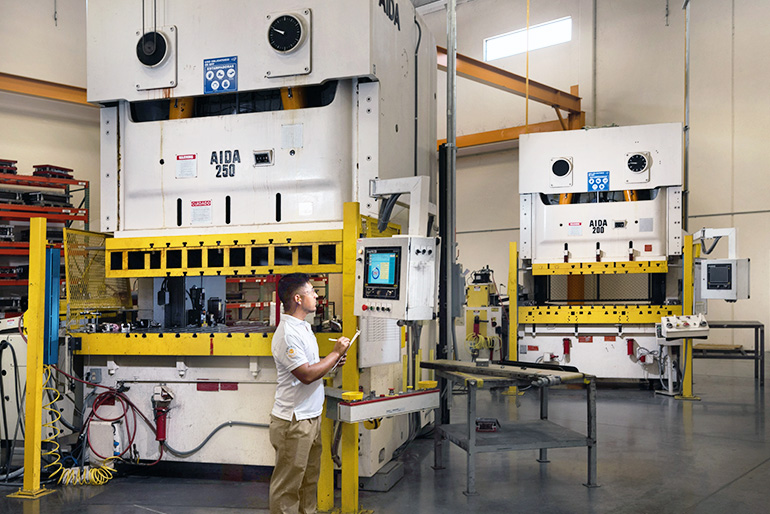
Final Thought
Layout considerations, prototyping, tooling, tools, production procedures, and high quality control are essential elements of metal stamping. With its prevalent applications and market understandings, metal marking proceeds to be a flexible and reliable manufacturing procedure.